Concrete repair is the process of restoring concrete that has deteriorated due to factors like environmental conditions, load stress, or poor construction practices.
The intent behind concrete repair can vary from the need to improve aesthetics rather than function. For example, repairing cracks and erosion in a driveway restores the appearance and stops further surface damage. This damage doesn’t pose a significant threat to safety.
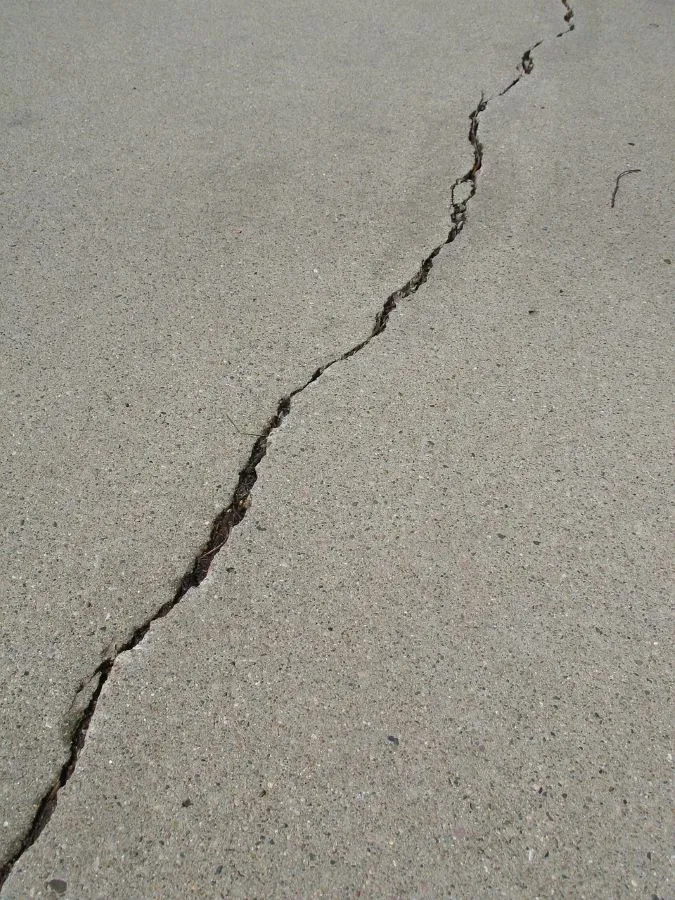
Yet, when it comes to concrete damage in critical structures like buildings, or bridges, repairs are necessary for safety and lives.
Table of Contents
Damage Assessment
Identifying the Type of Concrete Damage
Accurate identification of concrete damage is the first step for an effective repair strategy.
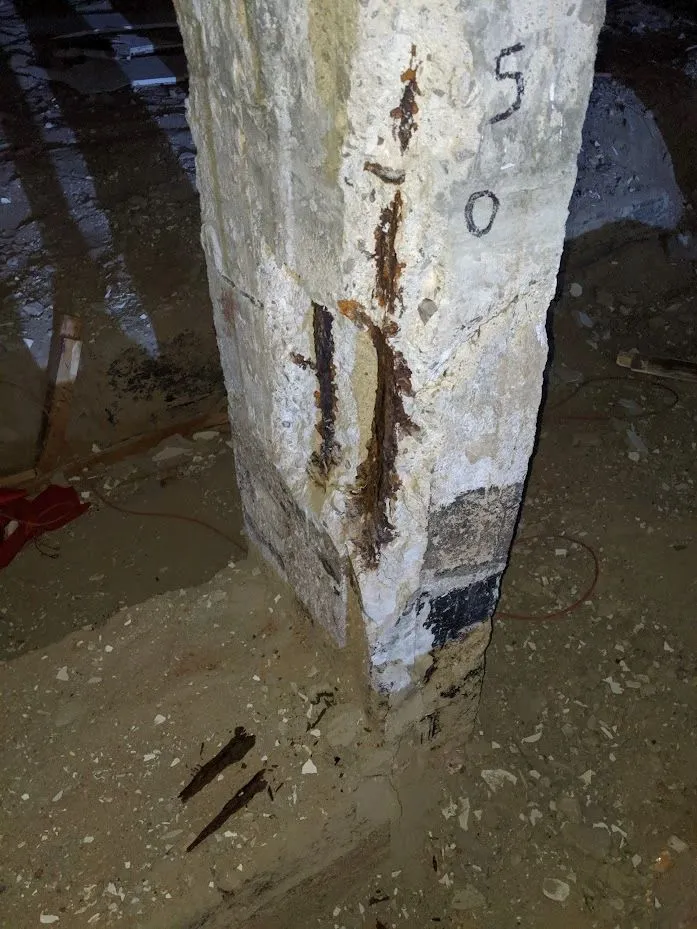
- Hairline or Shrinkage cracks are superficial and often result from shrinkage as concrete cures. it can appear soon after the concrete is placed and cured due to moisture loss.
- Structural cracks are more severe and show stress or load issues that threaten the structure’s integrity.
- Spalling flaking or breaking off the concrete surface, due to freeze-thaw cycles, mechanical impacts, or corrosion of embedded steel.
- Corrosion of reinforcement where steel rebar within the concrete rusts, expands and causes cracking, which weakens the structure. Each type of damage requires specific attention and repair methods to restore the concrete’s strength.
Determining the Cause of Concrete Damage
Understanding the causes of concrete damage is essential for developing effective repair solutions.
- Poor construction practices: such as inadequate mixing, improper curing, or insufficient reinforcement can lead to concrete failure.
- Foundation settlement: can cause uneven stress distribution, resulting in cracks and structural instability.
- Water infiltration: moisture can penetrate the concrete, leading to internal corrosion of reinforcement.
- Freeze-thaw cycles: damage in colder climates, where water within the concrete freezes and expands, causing cracks.
- Overloading: occurs when the structure is subjected to weight or stress more than its designed capacity. This leads to significant cracks and potential structural failure.
Evaluating the Extent of Damage
By assessing the depth and size of the affected area and understanding the potential structural implications.
The depth and size of cracks or spalling can state the severity of the damage. superficial damage might only need minor repairs. Deep, extensive cracks can suggest significant underlying issues.
Structural implications to determine whether the integrity of the entire structure is compromised. For example, surface cracks might not affect structural performance, but deep structural cracks or widespread spalling that exposes reinforcement bars can threaten the stability of the structure. Evaluation involves visual inspection, non-destructive testing methods like ultrasonic pulse velocity, and, in severe cases, core sampling to understand the internal condition of the concrete. Accurate assessment ensures that the repair strategy addresses the symptoms and root causes of the damage.
Concrete Repair Planning
- Cracks, epoxy injection where epoxy resins are injected into the cracks to bond the concrete back together and restore its structural capacity.
- Patching is suitable for addressing spalling and delamination; cleaning the damaged area and applying a repair mortar or concrete mix to fill and seal the damaged concrete.
- For large areas of damaged concrete, shotcrete application is ideal. Shotcrete is spraying a mix of concrete or mortar onto the surface, providing a strong, cohesive repair layer.
- Concrete overlays: for worn surfaces to improve their appearance and durability by adding a new layer of concrete or polymer-modified material over the existing surface.
- Reinforcement corrosion, cathodic protection is a specialized technique that uses electrical currents to prevent further corrosion of steel reinforcement within the concrete. This method is used for poor concrete that can’t be replaced.
- Each method is selected based on the specific type and extent of damage, ensuring the most effective repair solution.
Concrete Repair Execution
Surface Preparation
All repair materials manufacturers emphasize the importance of surface preparation.
- This process begins with loose and damaged concrete removal to create a stable base for the repair materials. This prevents future delamination and ensures good adhesion.
- Cleaning and roughening the repair area using wire brushing, sandblasting, or high-pressure water jets to remove contaminants like dirt, oil, and old coatings. This provides a textured surface that enhances the bonding of the new material (mechanical bonding).
- Reinforcing steel: expose the reinforcing steel and remove any rust or corrosion. Chip away the concrete around the rebar and treat the steel with rust inhibitors or protective coatings to prevent future corrosion.
Material Selection
Match the existing concrete properties by selecting materials that align with the properties of the existing concrete and reinforcement.
Reinforcement Repair
Cleaning the exposed steel, removing rust, scale, and any loose material using wire brushing, or sandblasting. Once cleaned, the steel must be treated with protective coatings to prevent future corrosion. For example, zinc-rich primers, epoxy coatings, or corrosion inhibitors, which create a barrier against corrosive agents.
Application of the Chosen Concrete Repair Method
Following the manufacturer’s instructions for material use and guidelines on the proportions, mixing times, and application conditions for optimal performance.
Placement techniques, for instance, epoxy injection, the epoxy must be injected slowly to ensure it penetrates the cracks. Patching requires the repair mortar to be compacted to remove air pockets and ensure a solid bond. For large-scale applications, mortar should be applied in layers to prevent sagging.
Curing Procedures
Proper moisture content allows the concrete to achieve its full strength and durability.
Quality Control and Inspection
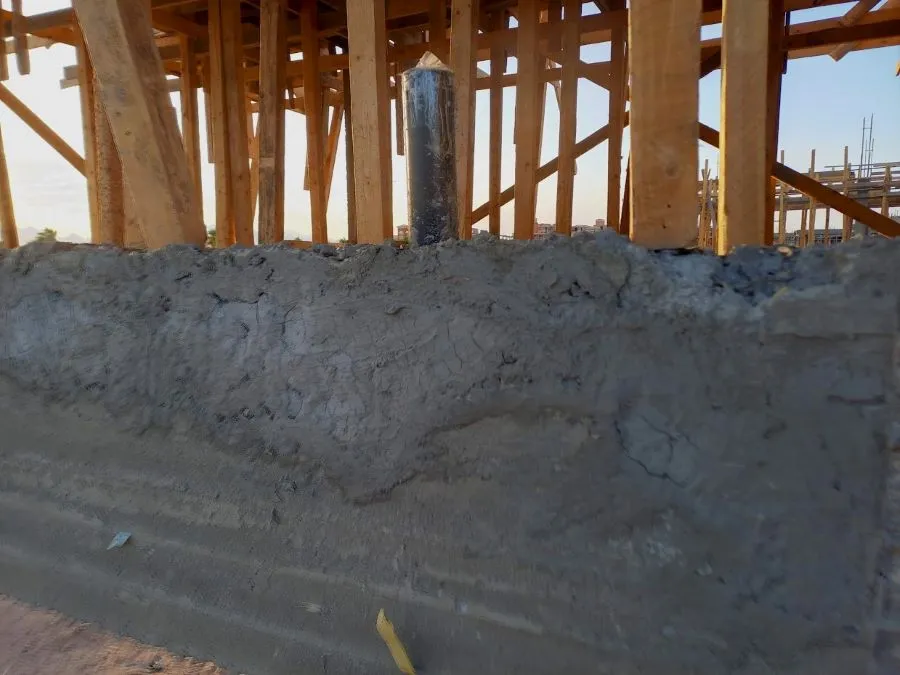
Visual Inspection
Inspectors start by checking for proper bond and finish, confirming the repair material is well-bonded with old concrete. Inspectors look for surface defects such as cracks, air bubbles, or uneven areas.
Non-Destructive Testing (optional)
In some cases, non-destructive testing (NDT) is used to determine the repair quality without damaging the structure. NDT methods, such as hammer testing or ultrasonic testing, are used to identify subsurface flaws or voids that are not visible to the naked eye. Hammer testing involves tapping the surface and listening for changes in sound that indicate hollow areas. Ultrasonic testing uses high-frequency sound waves to detect inconsistencies within the concrete.
Safety Considerations
- Personal Protective Equipment (PPE), such as gloves, safety glasses, and hard hats.
- Dust control measures inhalation risks must be eliminated for a safe working environment. This can include using water sprays or vacuum systems to collect dust generated during surface preparation.
- Working with hazardous materials like epoxies and other chemicals follow safety guidelines for handling and disposal. Adhere to material safety data sheet (MSDS) recommendations.
For more on safety
Conclusion
In conclusion, timely concrete repair extends the lifespan of concrete structures. Ongoing monitoring and maintenance plans to prevent future damage and preserve structural health. Following these best practices maximizes the lifespan of concrete structures.